CC2 Phase IV Instrumentation Plan
Instrumentation was also used to evaluate rigid pavement responses under aircraft loading. A total of 282 sensors were installed in CC2 Phase IV including: Vertical Displacement Transducers (VDTs); Horizontal Displacement Transducers (HDTs); Joint Gauges (Js); Thermistors (RH-Temps); Concrete Strain Gauges (CSGs); Soil Moisture Gages (SMs); and Relative Humidity gauges (RHs).
There were three procedures which helped to safeguard the sensors during concrete placement:
1. The instrumentation system was designed such that the majority of the sensors, for each test item, were embedded in the concrete during the placement of the first set of ten slabs.
2. The pump and boom deposited the concrete in open areas free of the sensor locations.
3. The sensors were hand packed and covered with concrete prior to additional material being placed above them.
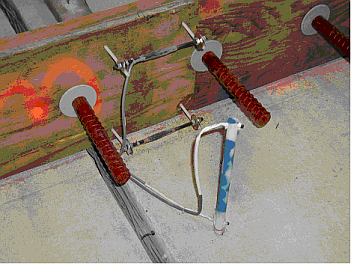
Eleven outages were experienced in the sensors as a result of the concrete placement and the responses from an additional eleven sensors appeared to be impacted by the construction process. Click here to download CC2 Phase IV sensor information including sensor types, sensor locations, and orientation.
Back to CC2 Phase IV Test Items