Airport paving materials—including asphalt, concrete, soils, and aggregates—undergo rigorous, complex stress from aircraft loads and endure harsh environmental conditions over extended periods. The industry is also expected to continue developing longer-lasting, more sustainable airport pavement materials. Researchers require laboratory testing to characterize traditional and innovative materials across various scenarios to comprehend how traffic and environmental conditions affect the pavement performance.
The FAA NextGen Pavement Materials Laboratory supports the National Airport Pavement Test Facility (NAPTF) and the National Airport Pavement and Materials Research Center (NAPMRC) in meeting their materials testing requirements. The laboratory possesses the necessary capabilities to examine the physical and mechanical properties of pavement materials before, during, and after accelerated pavement testing conducted at NAPTF and NAPMRC.
Since its establishment in 2010, the laboratory has furnished comprehensive material characterization data via a wide range of conventional and emerging test procedures. This 5,500 sq.ft. (510.97 sq. meter) facility is fully equipped for testing asphalt, concrete, soils, and aggregate materials used in airport pavement construction. All laboratory equipment is carefully maintained and calibrated to comply with accreditation requirements. The laboratory is accredited by the AASHTO Accreditation Program (AAP).
To bolster cutting-edge airport pavement research at ATR, the NextGen Pavement Materials Laboratory houses a diverse range of specialized equipment. Below are examples of the advanced testing methods conducted within the NextGen Laboratory:
|
Rutting in asphalt occurs when vertical deformation accumulates over time, resulting in a visible depression in the path of aircraft wheels. Asphalt Pavement Analyzers (APA) assess the susceptibility of asphalt mixtures to rutting by simulating dynamic wheel loads through a pressurized hose. While a standard APA employs a hose pressure of 100 psi, which is typical of highway tire pressures, the FAA’s custom Airport Pavement Analyzer tests at 250 psi to replicate tire pressures exerted by aircraft landing gears. Research conducted with this equipment has led to the development of a new standard for asphalt mixture design testing standard and is integrated into FAA Standards for Specifying Airport Construction (AC 150/5370-10).
|
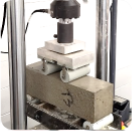
|
Repeated stresses under mechanical loading on pavements result in fatigue. The development of fatigue cracking can significantly reduce pavement performance and reduce the service life. To mimic the fatigue experienced by rigid (concrete) airfield pavements, a concrete fatigue beam apparatus subjects a concrete beam to aircraft-like bending loads. The apparatus utilizes four bearing blocks to secure the beam, establishing one loading line and two support lines at equidistant positions along the beam (third-point loading). Fatigue is induced by cyclic loads applied to two center blocks, set at a specified percentage of the sample’s breaking strength. After a certain number of cycles, the beam experiences sudden rupture. Several beams from the same slab are typically tested and the average number of loading cycles until the beam failure provides an estimation of the fatigue life of a concrete pavement slab under similar loads.
|
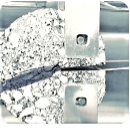
|
Winter temperatures, in conjunction with the aging of asphalt, contribute to the occurrence of low-temperature cracking in asphalt pavements. Low temperatures cause the pavement to contract, creating stresses that can lead to cracking if they overcome the strength of the asphalt layer. This can happen once or after multiple cooling and heating cycles. FAA employs an advanced technique known as the Disk-shaped Compact Tension (DCT) test to assess the asphalt mixtures’ capacity to withstand low-temperature cracking. In this test, the specimen is initially acclimatized within an environmental chamber at a controlled temperature. Subsequently, a pulling force (tension) is applied to a notch in the sample at a constant rate of crack mouth opening displacement. Sensors continuously monitor displacement throughout the test. The resistance to fracture is determined by measuring the peak load and fracture energy, which represents the energy needed to create a unit surface area of a crack in the test specimen.
|
Accreditations
ATR incorporates industry standards into the research process and depends on the NextGen Pavement Materials Laboratory to ensure quality and validate scientific findings.
The NextGen Pavement Materials Laboratory has actively participated in the AASHTO re:source and the Cement and Concrete Reference Laboratory (CCRL) Proficiency Sample and Laboratory Assessment Programs since 2013. The participation of laboratories in proficiency and on-site assessments enables the evaluation of the laboratory's testing quality and consistency by assessing its quality systems, testing equipment, and adherence to specific laboratory standards. Under the AAP, the FAA NextGen Laboratory is accredited for more than 50 standards, including protocols for asphalt, concrete, soil, and aggregates.
Collectively, these initiatives provide the essential tools for conducting high-quality and proficient onsite testing, thus enhancing the effectiveness of the FAA’s airport pavement research program.
Click here to view our accreditations.
In 2016, the NextGen Pavement Materials Laboratory was dedicated in honor of Jeffrey Rapol’s memory. Rapol, a dedicated FAA civil engineer, was a member of FAA Headquarter Pavement Engineering Team. He played a pivotal role in establishing both the laboratory and the NAPTF.